After reading John Forsythe's story of the restoration of his Bell Boy 404 Express and learning so much from it I thought I should do the same with my winter project. I purchased this boat back in January 2012 but haven't really had much time to work on her till now. As I go I'll keep pictures and hopefully get some more useful advice as I move along.
Here is a picture of the boat as she was when i picked her up from a tow lot earlier this year. She has a factory hardtop as well as the original curved glass windshield.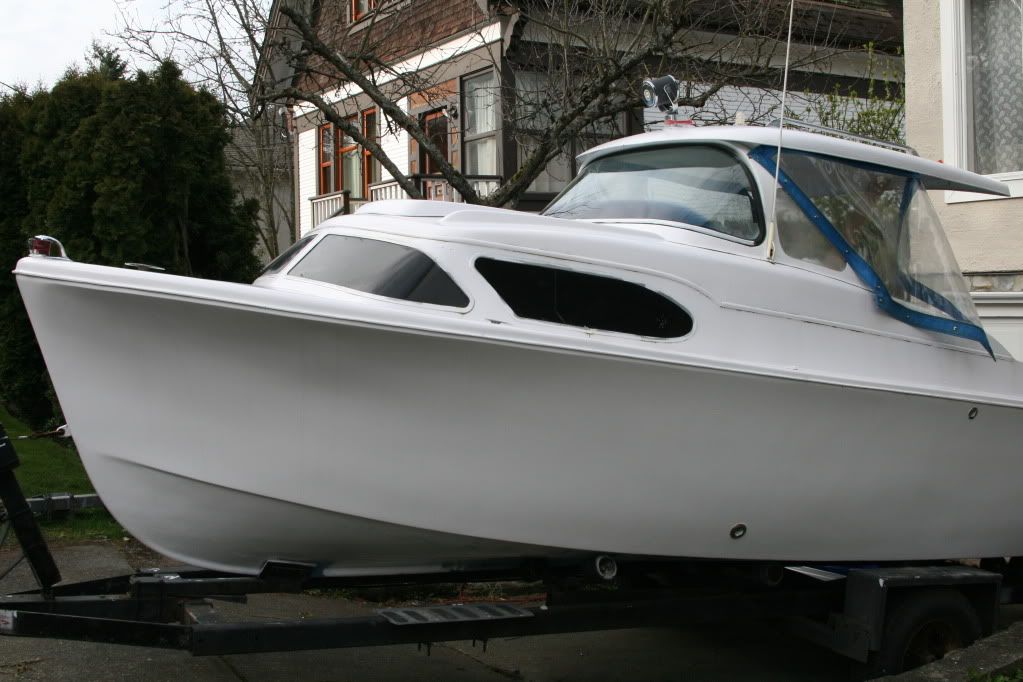
I've taken out the original fiberglass fuel tanks and will make an attempt this winter at cutting them open and lining them as I like both the light weight characteristic and the fact they are saddle tanks which help to maximize floor and storage space. I've also read that having the weight distributed on the sides of the boat adds to the stability as it takes more energy to get the boat rocking than a bottom heavy boat.

Here are some pictures of the inside configuration.
There is a space for a porta potty and a sink on the other side.

I'm assuming there is a water holding tank inside that other fiberglass dash but I can't for the life of me figure out how to open it up!

I'll have to take it apart to really figure it out. I'm sure there must be ruled now that don't allow these toilets to just drain directly through an open pipe to the water. What is the new standard for toilets on the water? Removable porta potty? What have some of you done?
My immediate plan is to redo the floor. I'll be keeping the back under the splashwell open for a bilge area and then putting down new floor, with foam and drainage as suggested here. Today I started taking out the floor.




After clearing out the bulkhead and cleaning up the space I decided on to try a carpentry trick suggested to me by a relative who is a cabinetmaker but has done a little work on the side helping out an old shipwright. What I've done here is bought an 4 x 8 door skin and laid it out on the old floor before I removed it. Then you take a framing square and line it up against the hull marking it out on the skin by tracing the shape of the square. Now when I get the new plywood I can create a trace of the exact shape I'll need by replotting those points using this skin as guide. I'll post more pictures when I get to that part.



There are a couple of things that have confused me as I started taking the floor up and I hope some other Skagit owners can shed some light on this. First of all I was surprised that the floor in the cuddy was lower than the floor on the boat and that what I thought were the stringers actually appear to be just floor joists. In between the joists there are some shorter smaller stringers (or at least thats what I'm calling them) that do run the whole length of the boat.



My question here is are those joists structural stringers or not? Wouln't having them stop at the cabin bulkhead weaken the overall structure of the boat? The bulkhead runs all the way to the floor but it really didn't seem to have much structural strength. I'm wondering if in the rebuild if I should link those stringers (joists?) together in order to make a stronger hull. Some insight here would be appreciated.
A second thing that concerned me is that it looks like there was a fire in the boat at some time. Some of the stringers were burned right through.


It also seemed odd to me that they were only 1 sided - is this normal? Aside from the middle stringer which was glassed all the way around, the other side ones only had glass and cloth on the inside wall. The outside is open.


Again it makes me wonder if this is just because what I think are stringers are really just floor joists for supporting the floor?
Here is a picture of the boat as she was when i picked her up from a tow lot earlier this year. She has a factory hardtop as well as the original curved glass windshield.
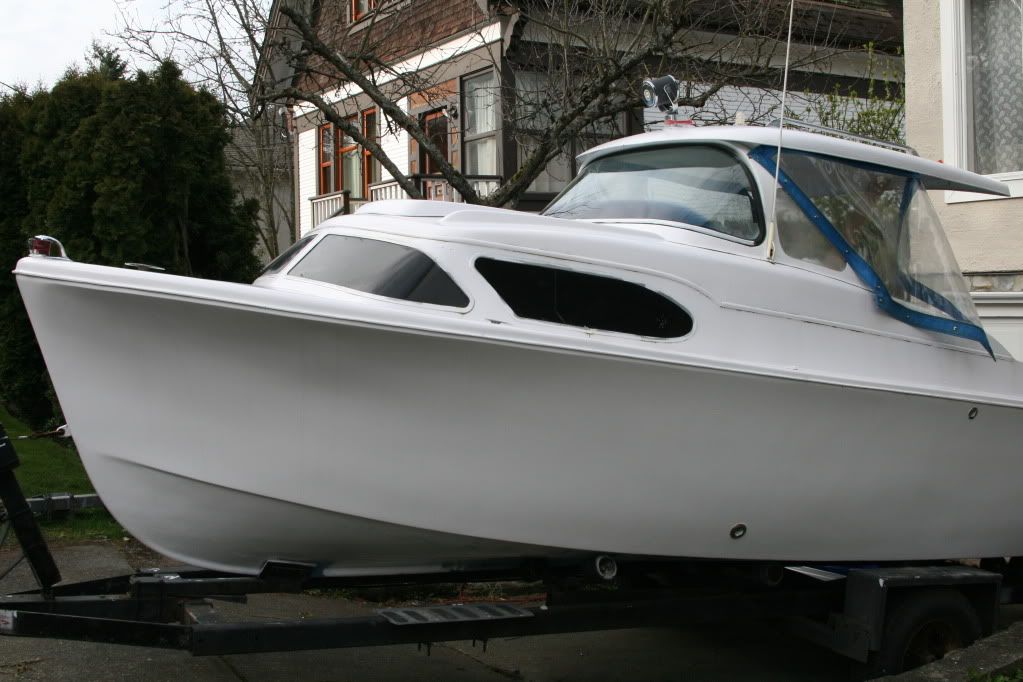
I've taken out the original fiberglass fuel tanks and will make an attempt this winter at cutting them open and lining them as I like both the light weight characteristic and the fact they are saddle tanks which help to maximize floor and storage space. I've also read that having the weight distributed on the sides of the boat adds to the stability as it takes more energy to get the boat rocking than a bottom heavy boat.


Here are some pictures of the inside configuration.

There is a space for a porta potty and a sink on the other side.

I'm assuming there is a water holding tank inside that other fiberglass dash but I can't for the life of me figure out how to open it up!

I'll have to take it apart to really figure it out. I'm sure there must be ruled now that don't allow these toilets to just drain directly through an open pipe to the water. What is the new standard for toilets on the water? Removable porta potty? What have some of you done?
My immediate plan is to redo the floor. I'll be keeping the back under the splashwell open for a bilge area and then putting down new floor, with foam and drainage as suggested here. Today I started taking out the floor.




After clearing out the bulkhead and cleaning up the space I decided on to try a carpentry trick suggested to me by a relative who is a cabinetmaker but has done a little work on the side helping out an old shipwright. What I've done here is bought an 4 x 8 door skin and laid it out on the old floor before I removed it. Then you take a framing square and line it up against the hull marking it out on the skin by tracing the shape of the square. Now when I get the new plywood I can create a trace of the exact shape I'll need by replotting those points using this skin as guide. I'll post more pictures when I get to that part.



There are a couple of things that have confused me as I started taking the floor up and I hope some other Skagit owners can shed some light on this. First of all I was surprised that the floor in the cuddy was lower than the floor on the boat and that what I thought were the stringers actually appear to be just floor joists. In between the joists there are some shorter smaller stringers (or at least thats what I'm calling them) that do run the whole length of the boat.



My question here is are those joists structural stringers or not? Wouln't having them stop at the cabin bulkhead weaken the overall structure of the boat? The bulkhead runs all the way to the floor but it really didn't seem to have much structural strength. I'm wondering if in the rebuild if I should link those stringers (joists?) together in order to make a stronger hull. Some insight here would be appreciated.
A second thing that concerned me is that it looks like there was a fire in the boat at some time. Some of the stringers were burned right through.


It also seemed odd to me that they were only 1 sided - is this normal? Aside from the middle stringer which was glassed all the way around, the other side ones only had glass and cloth on the inside wall. The outside is open.


Again it makes me wonder if this is just because what I think are stringers are really just floor joists for supporting the floor?
Comment